The path to the finished product
Methods of construction
Knierim’s experienced engineers design steel substructures for customized moulds. Thanks to the cooperation with Knierim Yachtbau, Knierim Tooling can offer further services such as manufacturing fitting pieces, heating and cooling facilities.
The steel substructure will be covered with plywood on which a laminate made of multiple layers of E-glass with epoxy resin will be applied. For the next layer 50 mm of contoured balsa core and/or PVC foam is used. It is glued with epoxy resin using vacuum technology.
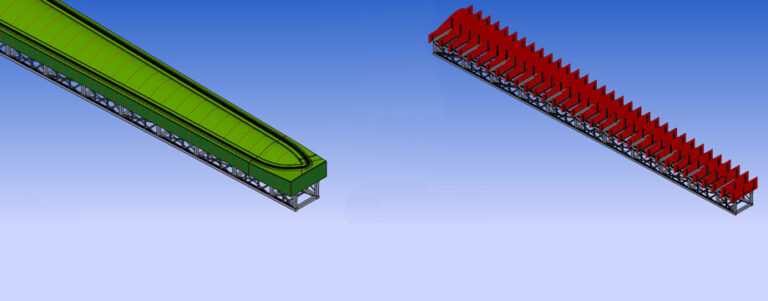
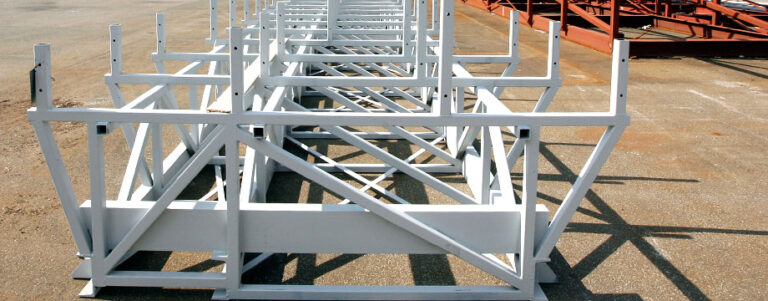
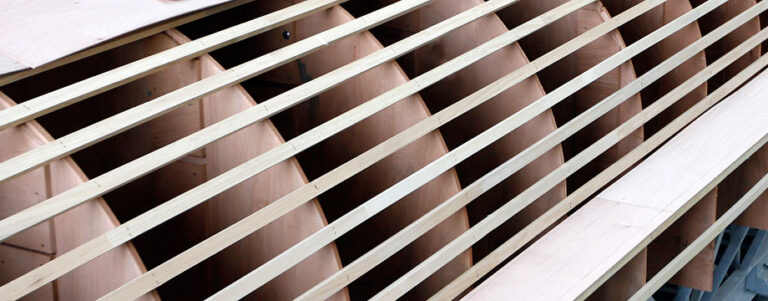

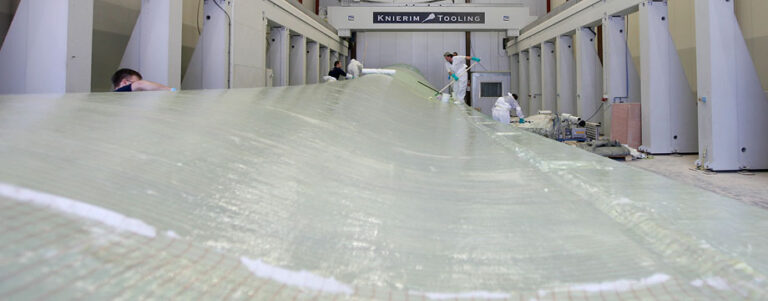
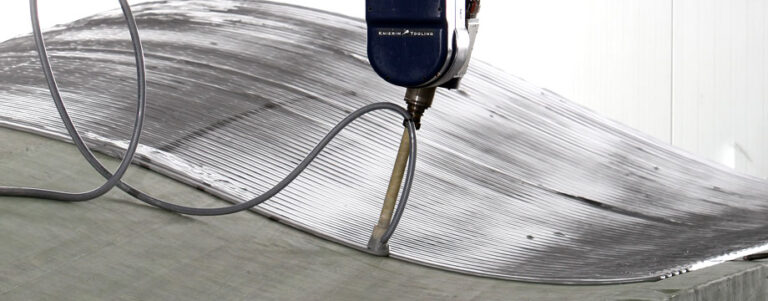
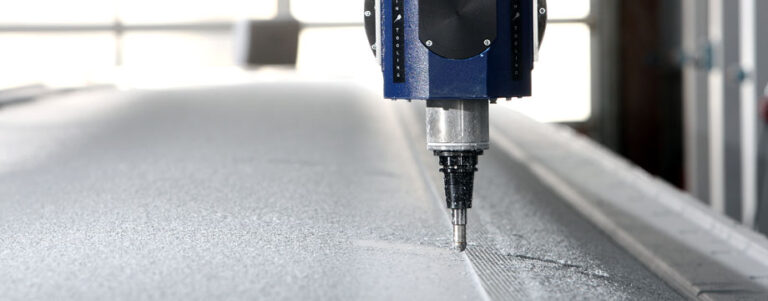
The core material will be machined before the next layer is laminated with E-glass and epoxy resin. Next is a vacuum test followed by the application of a high quality epoxy paste. Knierim Tooling uses premium pastes of renowned producers. Highly accurate paste application minimizes material waste and optimizes finishing times.
The paste will be precisely machined to the required geometry before scratch lines and marks are set. The last job is finishing the surface to customer’s needs in the range from sanding with P240 to polished EP or VE primer.
Thanks to the close co-operation with Knierim Yachtbau, Knierim Tooling can also offer services such as the manufacture of add-on parts, heaters and cooling systems.